銅箔外形激光切割機速度慢如何調快
以下是針對銅箔外形激光切割機提速的系統性優化方案,結合設備參數、工藝調整及生產管理,總計約800字:
一、設備參數優化(核心提速手段)
1.激光功率與波形調整
-峰值功率提升:在設備安全范圍內提高峰值功率(例如從2000W增至2500W),縮短單點熔化時間。
-脈沖頻率優化:銅箔導熱快,需高頻率脈沖(建議150-250kHz)實現連續切割,避免熱量堆積導致燒邊。
-占空比調節:適當降低占空比(如30%→20%),減少熱影響區,允許更高移動速度。
2.切割速度與加速度
-最大速度設置:將切割速度提升至設備極限(如從100mm/s提至150mm/s),需同步調整加速度(≥1.5G)以縮短啟停時間。
-拐角減速補償:啟用“預判減速”功能,降低拐角速度損失(例如由70%降至50%)。
3.光路與聚焦優化
-動態聚焦校準:確保不同位置光斑直徑≤0.03mm,能量密度提升可提速20%以上。
-保護鏡片清潔:每日清潔鏡片,透光率下降10%會導致速度損失15%。
二、工藝策略優化(減少無效時間)
1.路徑規劃升級
-共邊切割:相鄰圖形共享切割線,減少空移路徑(效率提升15-30%)。
-空程優化算法:采用“最近鄰”算法規劃切割順序,縮短激光頭移動距離。
2.多圖形批處理
-嵌套排版:使用專業軟件(如AutoNEST)自動緊密排樣,材料利用率提升至90%+。
-群組切割:將小尺寸圖形分組,一次切割多個單元。
3.輔助工藝改進
-氣壓與氣體選擇:采用高壓空氣(≥0.8MPa)替代氮氣,快速吹除熔渣,避免二次灼燒。
-飛行切割技術:開啟連續加工模式(ContinuousCutting),激光頭不停頓切換圖形。
三、設備維護與硬件升級
1.關鍵部件狀態檢查
-導軌與絲杠潤滑:每月清洗并更換潤滑脂,摩擦阻力增大會導致加速度下降。
-激光器冷卻系統:確保水溫≤22℃(±1℃),功率波動控制在3%以內。
2.硬件升級選項
-高動態振鏡:升級至30m/s級振鏡,大幅提升定位速度。
-紫外激光源替換:若為紅外激光(1064nm),可更換為綠光(532nm)或紫外(355nm)激光器,銅吸收率提升3-5倍。
四、材料與環境的適配
1.銅箔預處理
-表面涂層:噴涂吸光材料(如納米石墨烯涂層),提升激光吸收率30%+。
-張力控制:保持箔材張力恒定(推薦20-30N),避免抖動導致重切。
2.環境控制
-溫濕度穩定:維持溫度23±2℃、濕度40-60%,防止光學部件熱變形。
-除塵系統:安裝負壓抽吸裝置,避免煙塵附著鏡片。
五、生產管理優化
-自動上下料系統:集成機械手換料,減少停機時間(節拍縮短30-60秒/片)。
-實時監控系統:加裝CCD視覺定位,自動補償材料偏移,省去人工校準時間。
-設備聯動:通過MES系統同步切割機與前后工序,消除等待空閑。
提速效果驗證與安全警告
-測試方法:
選取典型圖形(如100×100mm含10個圓孔),對比優化前后加工時間。
-安全紅線:
禁止為提速超限提高功率(>設備額定值110%),否則損傷激光器壽命!
-預期效果:
綜合優化后,加工速度可提升40-70%(原100mm/s→140-170mm/s),同時良率維持≥98%。
附:參數調整對照表示例
|參數項|原始值|優化值|作用|
||–|–|–|
|峰值功率|2000W|2400W|提升熔融效率|
|脈沖頻率|100kHz|200kHz|減少熱堆積|
|切割速度|100mm/s|150mm/s|直接縮短工時|
|加速度|1.0G|1.8G|減少啟停耗時|
|輔助氣壓|0.5MPa|0.9MPa|增強熔渣清除|
>提示:每次僅調整1-2個參數,記錄切割質量(毛刺高度≤0.05mm)與速度變化,逐步逼近最優解。建議保存多組工藝包,適配不同圖形復雜度。
通過以上多維度優化,可在保障質量的前提下顯著提升效率。如需具體參數調試指導,請提供設備型號(如IPG激光器/SIEMENS系統)及銅箔厚度,我將提供定制化方案。
點擊右側按鈕,了解更多激光打標機報價方案。
相關推薦
銅箔外形激光切割機速度慢如何調快一點
銅箔外形激光切割機速度慢如何調快一點
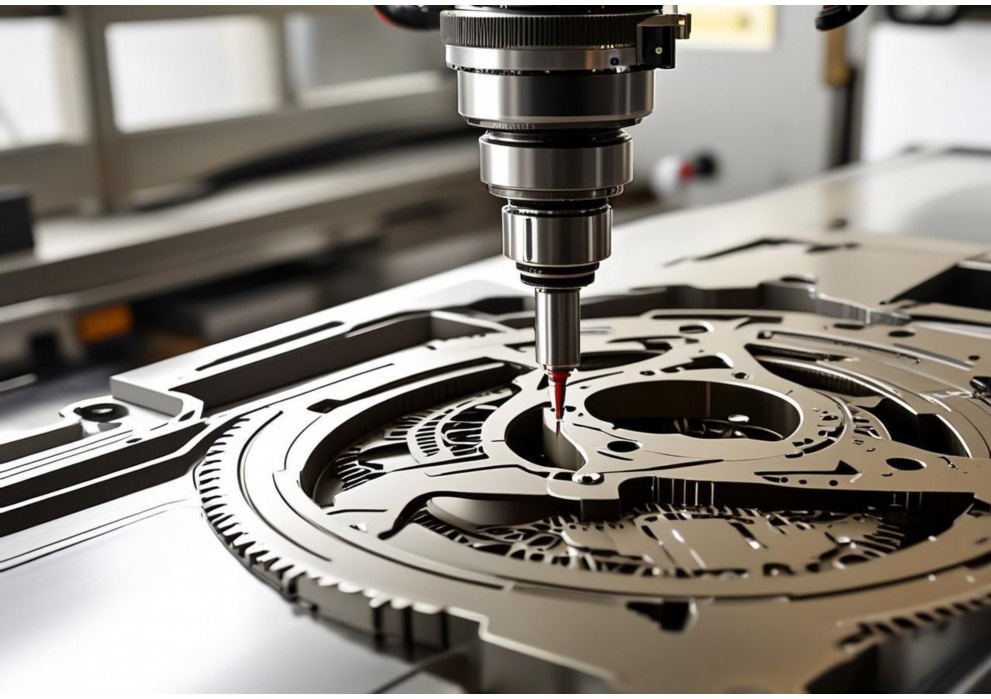
銅箔外形激光切割機速度提升優化方案
銅箔激光切割速度慢直接影響生產效率和成本。提升速度需要系統性地排查與優化多個關鍵環節,以下是具體策略:
一、激光參數精細調優(核心環節)
1.提升激光功率:
原理:更高功率密度能更快熔化/氣化銅箔,是實現高速切割的基礎。
操作:在設備允許范圍內,逐步增加激光功率(例如每次增加5-10%)。注意:需同步優化其他參數(特別是頻率和占空比)以避免燒焦、毛刺、熱影響區擴大。
2.優化脈沖頻率(Frequency):
原理:頻率決定單位時間內激光脈沖的數量。提高頻率通常能提高切割速度。
操作:嘗試逐步提高頻率。關鍵點:頻率過高可能導致單個脈沖能量不足(尤其在功率未同步提升時),無法有效切割或產生毛刺。需找到功率與頻率的最佳匹配點。
3.調整脈沖占空比(DutyCycle):
原理:占空比指一個脈沖周期內激光“開啟”時間的比例。增加占空比意味著在單位時間內有更多能量作用于材料。
操作:在保證不燒焦、切縫質量達標的前提下,嘗試適度增加占空比(例如每次增加5%)。
4.優化離焦量:
原理:焦點位置直接影響光斑大小和功率密度。對于極薄的銅箔,通常采用零焦或輕微正離焦(焦點在材料表面或略上方)以獲得更小的光斑和更高的能量密度,利于高速切割。
操作:進行離焦量測試(例如從-0.5mm到+0.5mm,步進0.1mm),找到切割速度最快且質量符合要求的位置。
5.減小光斑直徑(如適用):
原理:更小的光斑意味著更高的功率密度(功率/面積),能更快作用材料。
操作:若設備支持更換不同焦距的場鏡或擴束鏡組合,選擇焦距更短的場鏡(通常可獲得更小光斑)。注意:小光斑景深變短,對平臺平整度和調焦精度要求更高。
二、工藝氣體優化
1.確保氣壓充足穩定:
原理:輔助氣體(通常為壓縮空氣或氮氣)主要作用是吹走熔融物、冷卻切縫邊緣、抑制氧化。氣壓不足會導致熔渣清除不暢、熱量積聚,迫使降低速度以保證質量。
操作:檢查氣源壓力、減壓閥設定值、氣管有無泄漏或彎折。根據設備推薦值和實際切割效果,適當提高氣壓(特別是切割復雜輪廓或較厚銅箔時)。
2.優化噴嘴選擇與高度:
原理:噴嘴口徑和到工件的距離影響氣流形態和有效性。
操作:
選用合適孔徑的噴嘴(通常小孔徑更利于高速切割的聚焦氣流)。
精確調整噴嘴高度(通常在0.5-2mm范圍),確保氣流能有效覆蓋切割區域。高度過低易碰撞,過高則氣流發散。
三、設備狀態與路徑優化
1.維護光學系統:
原理:透鏡、反射鏡污染會顯著衰減激光能量,降低有效功率。
操作:定期(按設備手冊或實際使用頻率)使用專用工具和清潔劑清潔保護鏡片、聚焦鏡、反射鏡。檢查鏡片有無損傷,及時更換。
2.維護運動系統:
原理:導軌、絲杠/齒條、軸承等運動部件的磨損、潤滑不足或異物卡滯會增加運動阻力,限制最大加速度和速度。
操作:按設備手冊要求定期清潔、潤滑導軌和傳動部件。檢查聯軸器、電機是否正常。
3.優化切割路徑(CAM編程):
原理:合理的路徑規劃能減少空程移動時間、優化切割順序、減少頻繁加減速。
操作:
減少空程:優化排版,盡可能縮短激光頭在切割圖形間移動的距離。
平滑路徑:對小圓弧或復雜拐角處進行適當平滑處理(如小線段擬合),減少方向急劇變化導致的減速。
共邊切割:若圖形間距允許且不影響質量,嘗試共邊切割。
優化切割順序:選擇最短的總體移動路徑。
4.調整加速度與加加速度(Jerk):
原理:更高的加速度/加加速度允許設備更快達到設定速度并在拐角處更快轉向,減少加減速耗時。
操作:在設備控制系統參數中(需有權限),在保證運動平穩、不引起設備振動或丟步的前提下,逐步提高X/Y軸的加速度和加加速度參數值。這對切割復雜小圖形效果顯著。
5.優化激光開關控制:
原理:減少激光開啟/關閉的延遲時間,特別是在切割密集小圖形時。
操作:檢查并優化控制系統的激光開關延遲參數(如“提前出光”、“延遲關光”時間)。確保軟件在路徑拐點或短距離移動時能高效控制激光開關。
四、材料與外部因素
1.確認銅箔特性:
原理:不同純度、厚度、合金成分、表面涂層(如抗氧化層)的銅箔,其激光吸收率和熱傳導率不同,最佳切割參數也不同。
操作:明確所用銅箔的具體規格。如更換批次或供應商,需重新測試優化參數。
2.保障材料平整度:
原理:翹曲或不平整的銅箔會導致焦點位置變化,影響切割效率和一致性,迫使降低速度以適應。
操作:檢查上料和吸附系統,確保銅箔被均勻平整地吸附在工作臺上。檢查臺面清潔度和平整度。
優化策略總結與注意事項:
1.系統性:速度提升是多種因素共同作用的結果,需系統性地逐一排查和優化,而非僅調一兩個參數。
2.循序漸進:每次只調整一個參數(或密切相關的兩個,如功率和頻率),記錄調整前后的速度和質量(切邊光滑度、毛刺、熱影響區、燒焦等),進行對比分析。避免同時大幅改動多個參數導致問題復雜化。
3.質量優先:速度提升絕不能以犧牲切割質量為代價!必須確保切邊光滑無毛刺、無粘連、無過度燒焦/氧化、尺寸精度符合要求。銅箔切割的毛刺問題尤其需要關注。
4.設備極限:了解設備的理論最大速度和加速度限制。接近極限時提升空間有限,需考慮設備升級。
5.安全:調整參數(尤其是提高功率)和維護設備時,務必遵守安全操作規程,佩戴防護眼鏡。
6.維護保養:定期、規范的設備維護(光學清潔、運動部件潤滑、冷卻系統檢查)是保持設備性能穩定和高速切割的基礎。
實施步驟建議:
1.基線測試:記錄當前“慢速”狀態下的所有關鍵參數(功率、頻率、占空比、速度、氣壓、離焦量等)和切割質量、速度。
2.設備檢查:優先進行設備狀態檢查(光學清潔度、氣體氣壓/流量、運動部件狀態、材料平整度)。
3.參數調優:按照上述策略,從激光參數(功率->頻率->占空比->離焦量)開始,結合工藝氣體,逐步優化。每次調整后做切割測試并記錄結果。
4.路徑與運動優化:在激光參數優化到較佳狀態后,再著手優化切割路徑和運動參數(加速度/Jerk)。
5.驗證與固化:找到一組速度顯著提升且質量達標的參數組合后,進行多批次、長時間的穩定性驗證。將最優參數固化保存為對應材料的標準切割工藝。
通過以上綜合性的優化措施,通常能顯著提升銅箔激光切割機的加工速度。關鍵在于耐心測試、細致記錄、質量把關和持續維護。
注意:實際操作前請務必詳細閱讀設備操作手冊,并在必要時咨詢設備制造商或專業工藝工程師的意見。
點擊右側按鈕,了解更多激光打標機報價方案。
銅板激光切割機
銅板激光切割機
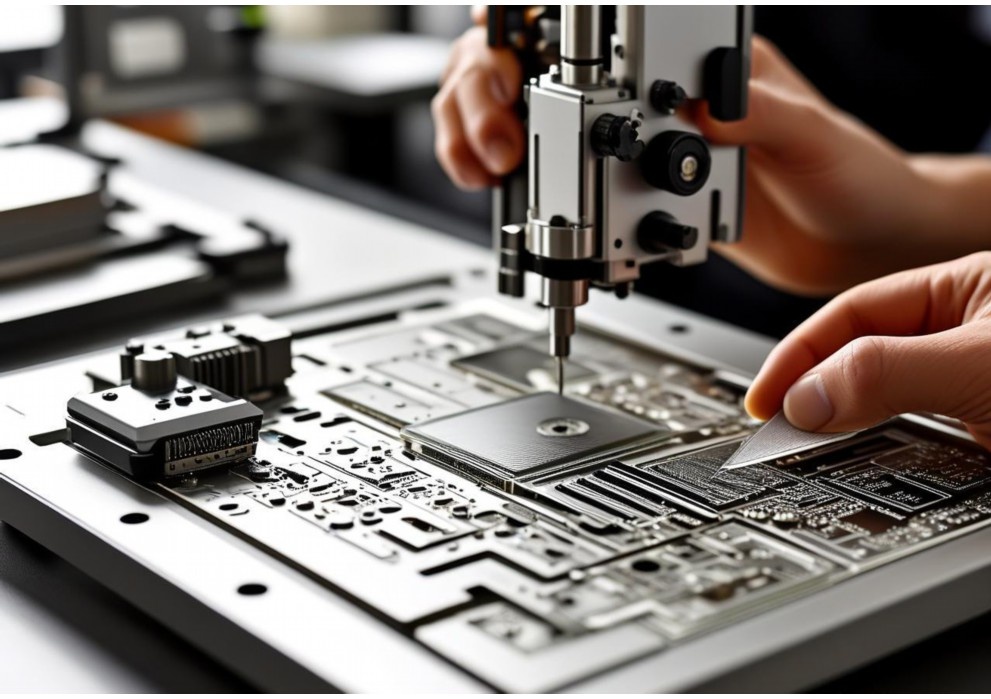
以下是一篇關于銅板激光切割機的詳細介紹,約800字,涵蓋其原理、特點、應用及選型要點:
銅板激光切割機:高效精密的金屬加工利器
一、技術原理
銅板激光切割機采用高能量密度的激光束照射銅板表面,通過瞬間熔融、汽化或氧化實現切割。針對銅的高反射特性,設備通常選用光纖激光器(波長1070nm)或更高效的綠光激光器(532nm),后者對銅的吸收率提升3倍以上,顯著減少反射損耗,確保切割穩定性。
二、核心優勢
1.高精度切割
激光聚焦光斑直徑可達0.01mm,切口寬度小于0.1mm,公差控制在±0.05mm內,適用于精密電子元件(如電路板接點、散熱片)。
2.無接觸加工
避免機械應力,保護銅板表面光潔度,尤其適合薄銅板(0.2-3mm)的復雜圖形切割。
3.效率提升
20mm厚銅板切割速度可達1.5m/min(6kW光纖激光),比傳統沖床效率提高50%以上。
4.柔性生產
CAD圖紙直接導入,30秒內切換圖案,適應小批量定制化需求。
三、關鍵技術配置
-激光源選擇:
-中厚板(≤8mm):6-12kW光纖激光器(經濟實用)
-超薄精密加工:500W綠光激光器(反射率降至5%以下)
-防反射系統:
配備反射光路徑監測及自動功率調節,防止高反射損傷光學元件。
-氣體輔助:
高純氮氣(99.99%)防止氧化,氬氣用于高光潔度切割。
四、典型應用場景
|行業|應用部件|加工要求|
|-|–|–|
|電力設備|銅母線、導電排|直角無毛刺,導電面平整|
|新能源|電池連接片、集流體|微孔群切割(φ0.5mm±0.05)|
|電子|電磁屏蔽罩、散熱基板|無變形雕刻(深度0.1mm)|
|裝飾工程|浮雕銅畫、建筑鑲板|曲線平滑,無熱影響區|
五、選型注意事項
1.材料兼容性:確認設備支持紫銅(T2)、黃銅(H62)等不同合金,黃銅需調節功率避免鋅揮發。
2.切割厚度匹配:
-3kW光纖激光:適用0.5-6mm銅板
-12kW光纖激光:可切割20mm厚銅板
3.除塵系統:必須配置高壓抽塵裝置,銅屑堆積易引發短路或火災。
4.軟件生態:選擇支持AI排料算法的系統(如HyperthermProNest),材料利用率提升15%。
六、行業發展趨勢
-復合加工:激光切割+焊接一體化設備逐步普及,減少工序轉移誤差。
-智能監控:實時熔池監測系統通過紅外傳感自動補償焦點位置,應對銅板熱變形。
-綠色制造:脈沖激光技術降低能耗30%,配合除塵凈化系統滿足ISO14000標準。
結語
銅板激光切割機憑借其無可替代的精度與靈活性,正推動電力電子、新能源等領域的制造升級。用戶選型時需綜合考量材料特性、產能需求及工藝擴展性,選擇適配的激光源與技術方案,方能最大化釋放設備潛力。隨著超快激光技術的成本下探,未來銅材加工將向微秒級超精細切割邁進。
點擊右側按鈕,了解更多激光打標機報價方案。
激光切割機切割銅片
激光切割機切割銅片
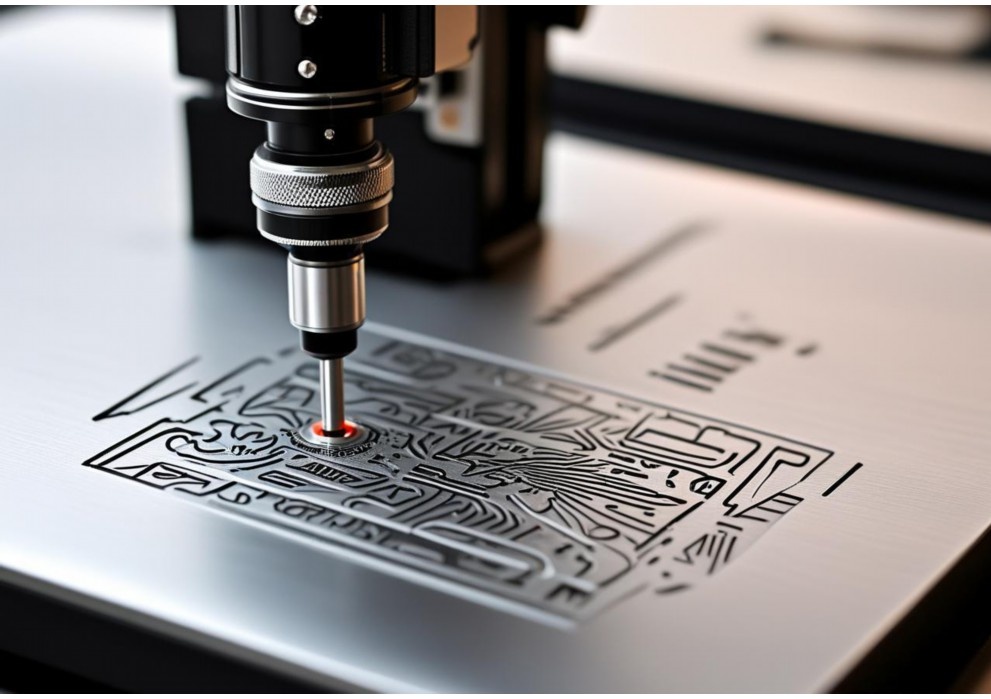
激光切割機精準駕馭銅片:技術、挑戰與突破
銅片憑借卓越的導電、導熱性及延展性,在電子、電力、新能源等領域扮演著關鍵角色。然而,其高反射率和高導熱性卻對傳統切割工藝構成嚴峻挑戰。激光切割技術憑借非接觸、高精度、高柔性等優勢,正逐步成為精密切割銅片的首選方案。
一、直面挑戰:銅的特性與切割難點
高反射率:銅對常見工業激光波長(如1μm左右的光纖激光)具有極強的反射性。這不僅大幅降低激光能量吸收效率,更可能導致反射光損毀激光器內部光學元件。
高導熱性:銅能迅速將局部吸收的激光熱量傳導擴散,使材料難以達到有效熔化或汽化所需的溫度閾值,顯著增加切割難度和能量消耗。
切口質量與氧化:切割時易在切口形成較厚的熱影響區,甚至產生熔融銅瘤、毛刺及氧化變色,影響精度和美觀。
薄片易變形:激光熱輸入可能導致薄銅片產生熱變形或翹曲。
二、技術應對:突破切割瓶頸
為克服上述困難,現代激光切割銅片技術已發展出針對性策略:
1.優選光源與波長:
高功率光纖激光器:成為主流選擇。通過提升峰值功率和優化光束模式(如BRIGHTMODE等技術),增強銅在近紅外波段的初始吸收率,克服反射壁壘。
綠光/紫外激光器:銅對更短波長(如綠光532nm,紫外355nm)吸收率顯著提高(可達~40%以上),尤其適用于超薄銅箔(<0.1mm)的精密切割,但設備成本和維護復雜度較高。 2.核心工藝參數精密調控: 高功率密度:采用高峰值功率、高光束質量激光器,結合小光斑聚焦,實現局部瞬間高溫,克服熱傳導。 高速切割:在保證切透前提下盡可能提高切割速度,縮短激光在單點作用時間,減少熱輸入和熱影響區。 優化脈沖參數:對于脈沖激光,精確控制脈沖寬度、頻率和能量,實現高效熔化和材料清除。 輔助氣體策略: 氮氣:最常用保護氣體,有效防止切口氧化,獲得光亮潔凈的切割面(尤其適用于紫銅、黃銅)。高純度高壓氮氣還能吹除熔渣。 氧氣:適用于較厚銅板(>3mm),利用氧化反應釋放額外熱量提升切割能力,但切口會氧化變黑,需后處理。
壓縮空氣:經濟方案,效果介于氮氣和氧氣之間,可能產生輕微氧化。
3.設備與輔助技術:
抗高反設計:激光器內部集成光束監控、反射光路徑隔離等防護機制,保障設備安全。
噴嘴優化:特殊設計的噴嘴確保輔助氣體精準、穩定、高壓地作用于切割前沿。
高度跟蹤與焦點控制:精密傳感器實時監控并調整噴嘴高度和焦點位置,確保切割過程穩定。
三、優勢顯著:激光切割銅片的競爭力
超凡精度:切縫窄(可達0.1mm以下),熱影響區小,輪廓精細,滿足微電子元件等高精度需求。
卓越柔性:無模具限制,通過軟件可瞬時切換切割任意復雜圖形,適配小批量、多品種生產。
非接觸加工:無機械應力,避免薄片變形;無刀具磨損,維護成本低。
高效清潔:高速切割結合合適氣體,切口光滑潔凈,減少后處理工序。
高度自動化:易于集成自動化上下料和在線檢測系統。
四、關鍵應用領域
電子電器:PCB/FPC導電線路、連接器端子、屏蔽罩、散熱片、電磁線圈、電池電極(極耳)。
新能源:光伏焊帶、電池結構件、電機定轉子硅鋼片中的銅部件。
精密儀器:傳感器元件、微電機部件、裝飾性金屬標牌/工藝品。
電力行業:特殊形狀的導電排、觸頭。
五、安全不容忽視
銅的高反射性使激光切割風險倍增。必須嚴格配備:
專業激光防護罩/房。
符合波長要求的激光防護眼鏡。
完善的安全聯鎖裝置。
操作人員需接受專業培訓,尤其警惕潛在的反射光危害。
結語
激光切割機已成為解鎖銅片精密加工潛力的關鍵鑰匙。通過優選激光源、精細調控工藝參數(功率、速度、氣體)以及應用抗反射等先進技術,激光切割有效克服了銅材加工的核心障礙,在電子、新能源等高精尖領域展現出無可比擬的效率與質量優勢。隨著激光技術的持續迭代,其在銅材加工領域的應用深度與廣度必將進一步拓展,推動相關產業升級。
點擊右側按鈕,了解更多激光打標機報價方案。
免責聲明
本文內容通過AI工具智能整合而成,僅供參考,博特激光不對內容的真實、準確或完整作任何形式的承諾。如有任何問題或意見,您可以通過聯系1224598712@qq.com進行反饋,博特激光科技收到您的反饋后將及時答復和處理。